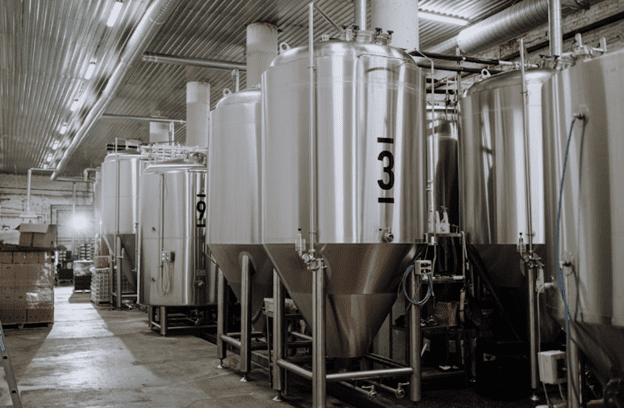
Manufacturing is one of the largest consumer freshwater consumers in the world, as approximately 20 % of the total freshwater withdrawals. Industries depend on water for cooling, cleaning and processing, and often consumes huge amounts that raise local resources. With climate change and population growth increased, manufacturers must rethink their approach to water use.
Many areas are already suffering from water shortages, forcing governments to impose tougher regulations on industrial water consumption. Companies that fail to address these concerns risk high costs, fines and possible disorders. However, companies that adopt water -saving operations can reduce expenditures, improve sustainability, and build a reputation as environmentally responsible institutions.
This article explores how manufacturers can reduce water waste through innovative technologies, smart strategies and sustainable production methods.
How manufacturing contributes to excessive use of water
Many industries use much more water than necessary because of the ineffective systems and old practices. In sectors such as textiles, food processing and chemical production, water is necessary for cleaning, cooling and mixing raw materials. However, a lot of this water goes to a waste due to leaks, ineffective equipment, or excessive unnecessary use.
Traditional cooling systems depend on huge amounts of water, and many manufacturing factories draining sewage without appropriate treatment. This leads to both excessive consumption and environmental pollution. Some companies continue to use one use water systems instead of investing in recycling technologies. Treating these aspects is necessary for long -term sustainability.
Using super focused formulas to reduce water use
One way to reduce the use of industrial water is via Drafting products To require less water. Many cleaning products, detergents and personal care elements are traditionally diluted with large quantities of water during manufacturing. By turning into Upperly concentrated formulasManufacturers can reduce both water use and packaging waste.
A great example of this approach is MillukaAl -Afia CompanyWho was a leader in Manufacturing responsible. Founded by Frank Vandrinklot, producing the company Cleaning products and personal care with superior focusReducing the need for excessive water in both production and consumer use. This strategy is not only reduced Water consumption But too Reduces plastic waste By requesting less filling. By adopting similar innovations, other manufacturers can significantly reduce the environmental imprint while maintaining high -quality products.
This approach benefits multiple areas of sustainability. With the use of less water in production, companies also reduce the amount of plastic and energy needed for packaging and transportation. Consumers are increasingly looking for sustainable products, making the concentrated formulas an attractive choice for companies who want to stay at the top of the market trends.
Cut water waste with advanced nomination and recycling
Many companies now adopt closed water systems, where water is treated and reused instead of disposing of it. The filtration technology allows manufacturers to remove pollutants and water recycling for frequent use of industrial processes. This greatly reduces the need for fresh water while reducing wastewater drainage.
Zld unloading systems (ZLD) It has become more common in industries that require large amounts of water. These systems are treated and repeated every drop, and no pure water left behind. Although initial investment can be high, companies provide long -term money by lowering water consumption and meeting regulatory standards.
The role of smart technology in preserving water
Technology plays an important role in improving water use in manufacturing. Many companies now use AI’s sensors and monitoring systems that support IOT to track actual time consumption. These tools help determine leaks, measure efficiency and control water use on the basis of demand.
By integrating smart technology, companies can discover and repair shortcomings before leading to excessive water waste. The automatic closure valves prevent unnecessary water flow, while predictive analyzes help to make better decisions on water customization. When these technologies become more affordable, more manufacturers integrate them into their sustainability strategies.
Sustainable cooling systems in factories
Cooling systems in industrial plants are among the largest consumers of water. Many traditional cooling towers require a continuous flow of water to prevent high temperature, which leads to excessive consumption and waste. To reduce this effect, manufacturers turn into air and hybrid cooling systems, which use water much less than traditional methods.
Eliminate the browned systems that are completely needed for water using fans to waste heat. The hybrid systems, on the other hand, combine air and water cooling to reduce water consumption in general. Many companies also use Cooling systems closed loopWhich recycle water instead of emptying it after using one. These methods not only maintain water, but also less than maintenance costs and improve energy efficiency.
Rain water harvesting and alternative water sources
Manufacturers are increasingly harvesting rainwater as an alternative to the use of municipal sources or groundwater. This practice allows companies to collect and store rain water for various industrial applications, such as cooling, cleaning and irrigation. Rain water harvest reduces dependence on fresh water supplies and helps industries to achieve water conservation goals.
In addition to rain water, some companies use gray water recycling-draining wastewater from drains, bathing and other non-industrial sources. This treated water can be reused for tasks that do not require drinking water, which reduces total consumption. By combining these solutions, manufacturers can significantly reduce their environmental effect while lowering operational costs.
Organizational pressure and pushing for water -saving manufacture
Governments all over the world apply tougher regulations to the use of industrial water. Many countries require manufacturers to reduce water waste, properly treat wastewater, and report their use data. Companions in compliance with heavy fines, operational restrictions, and reputable damage.
To remain at the forefront of these regulations, companies invest in sustainable water management practices. Some industries follow international standards such as ISO 14046 (water fingerprint assessment) and a LEED certificate (Energy Driving and Environmental Design), which encourage the use of responsible water. Adopting these frameworks helps companies avoid legal issues while improving their environmental credibility.
Reducing water pollution through the responsible wastewater management
Manufacturing not only consumes large amounts of water, but also contributes to pollution. Many industrial processes produce sewage filled with chemicals, heavy metals and other pollutants. If not treated, this wastewater can harm ecosystems and pose health risks to nearby communities.
To address this problem, companies implement advanced sewage treatment systems. These systems remove harmful substances before emptying the water again into the environment. Some manufacturers also participate in non -liquid discharge initiatives (ZLD), where all wastewater is treated and re -used instead of launching it. By taking these steps, companies can protect water resources while maintaining compliance with environmental laws.
Maintaining water is no longer an option for manufacturers – it is a necessity. With the increased shortage of water and the tightening of regulations, companies must adopt effective water management strategies to survive competitive and responsible.
By implementing closed ring systems, smart technology, sustainable cooling methods, and wastewater treatment solutions, manufacturers can significantly reduce water fingerprint. These efforts not only benefit the environment, but also lead to low costs, increase efficiency, and improve public perception.